Monday, June 22, 2015
Browse »
home»
Sheer Work Continues
Getting the sheers on the boat should have been easier than adding the chines. After all, the wood is thinner and more flexible. Steaming was easier because less mass needed to be heated. Curves created through steaming held their shape better than that of the chines.
But instead, the sheer presented their own challenges. Let it be understood that I am not complaining here. Rather, I am remarking on the necessity of adapting and working through problems and difficulties as they occur.
particular process started off well. I had steamed a second piece of lumber and bent it. It fit pretty good around the breasthook, and when I added the extra length via a scarf joint, I was able to easily bring the far end around to the boat.
The first challenge I noticed was that the angle of the breasthook sides and the notches made it difficult to line up the sheer between the breasthook and frames 6 and 5. But by clamping the wood to the breasthook, I determined that I could work in stages and get the wood to line up. Therefore I decided to glue the first lamination to the breasthook only, and then over the next several days, glue the lamination to single frame points. would allow me to take advantage of the rigidity of the already glued on sections and adjust the loose end as I went.
I accomplished this first glue up and then proudly displayed the photo for all to see. Pride hit number 1; a friend on the Glen L builders forum pointed out that the sheer appeared to be too far forward. If I were to have continued and glued the second lamination on at this point, it would have extended out past the breasthook.
In other words I had missed that I needed to have the sheer set back enough so that when the front of the stem was faired at an angle, the line from the faired stem would flow into the sheer. The way I had it mounted would have required me to remove nearly all the second lamination at the front of the boat. Of course this was unacceptable.
Examining the problem for awhile, I realized that the breasthook itself was mounted too far forward on the stem. looked like a disaster of major proportions and I was quite upset about this for an evening. But later after examining it some more and with the suggestions from the friend on the forum, I elected to cut the forward side of the breasthook back the necessary amount (about 5/8 inch).
First I had to cut the glued on sheer away from the breasthook. The Bosch multi-tool I recently purchased was perfect for doing this as well as cutting the breasthook back. After accomplishing this I hit the forward face of the breasthook with a belt sander to smooth it out. I could now reattach the sheers to the breasthook and they would be set back the correct amount.
Of course, the breasthook is now smaller and I intend to reinforce it on the back edge after the sheers are all in place. I will be laminating a solid piece of mahogany to the back edge of the breasthook between the sheers. should effectively restore any strength lost when I trimmed the forward edge.
So I re-attached the sheer to the breasthook and over the next three days, attached first frame 6, then frame 5, and then the remaining frames to the aft end of the boat. I adjusted the sheer each day as I attached it to another frame. The following photos show a bit of this process.
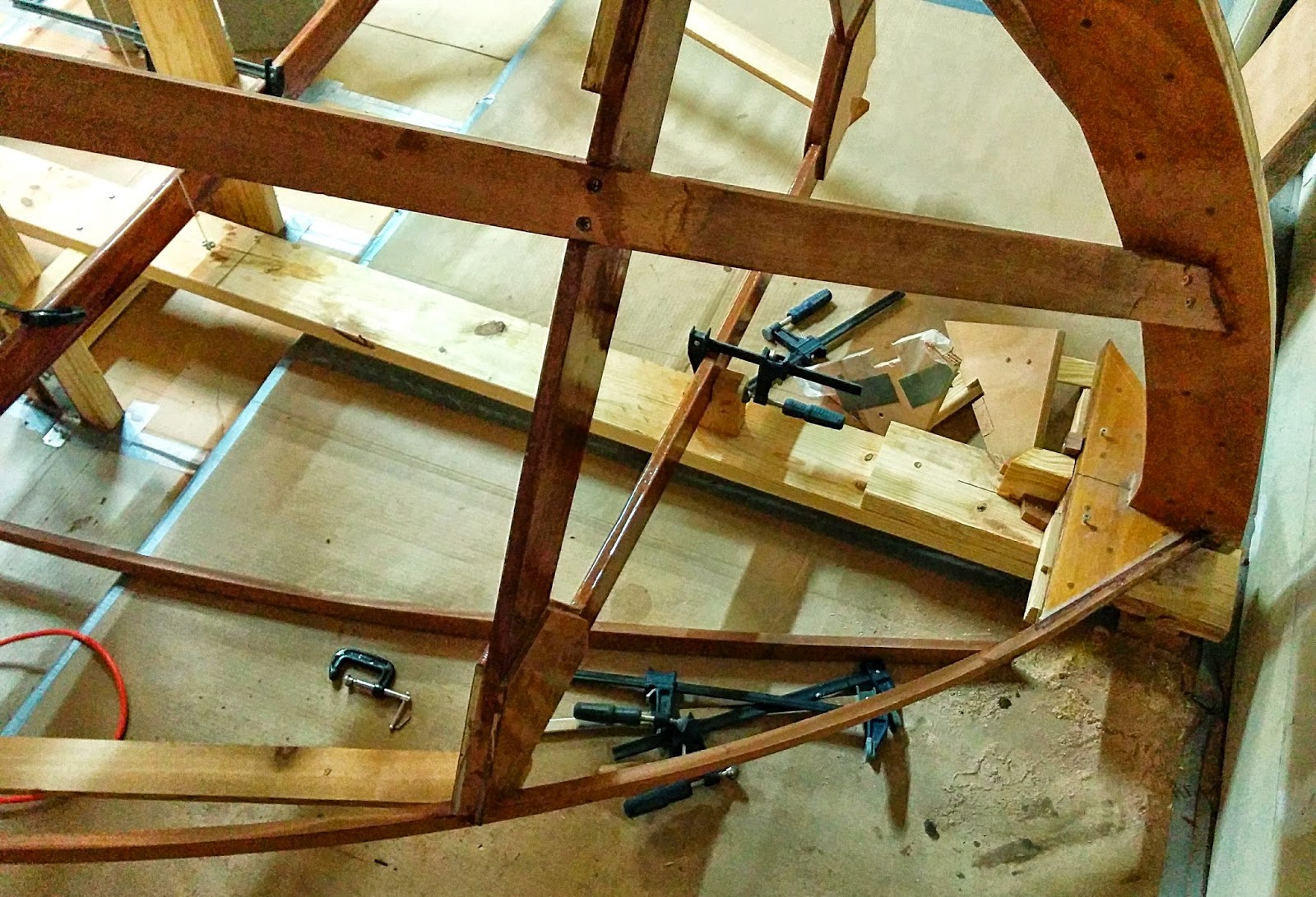
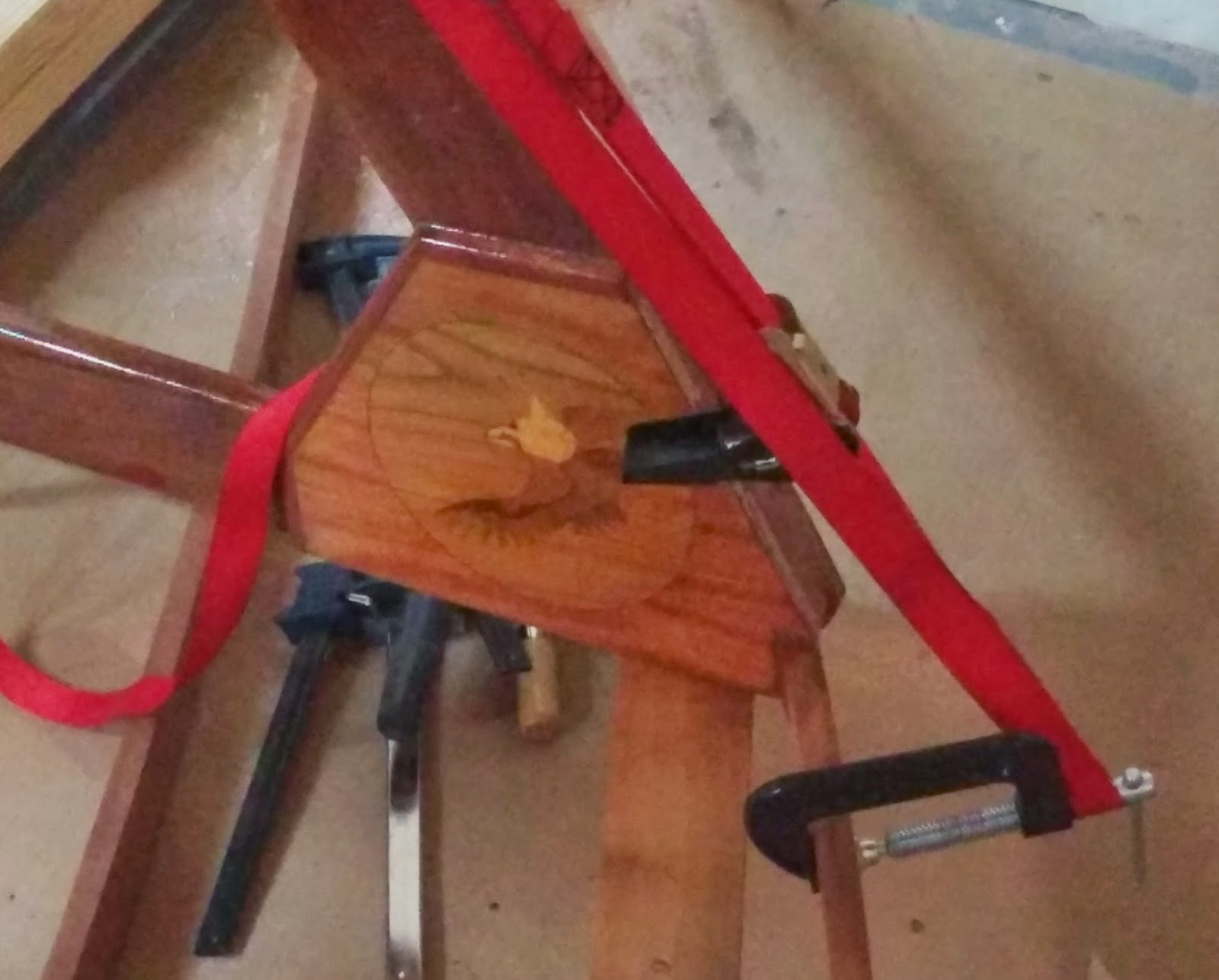
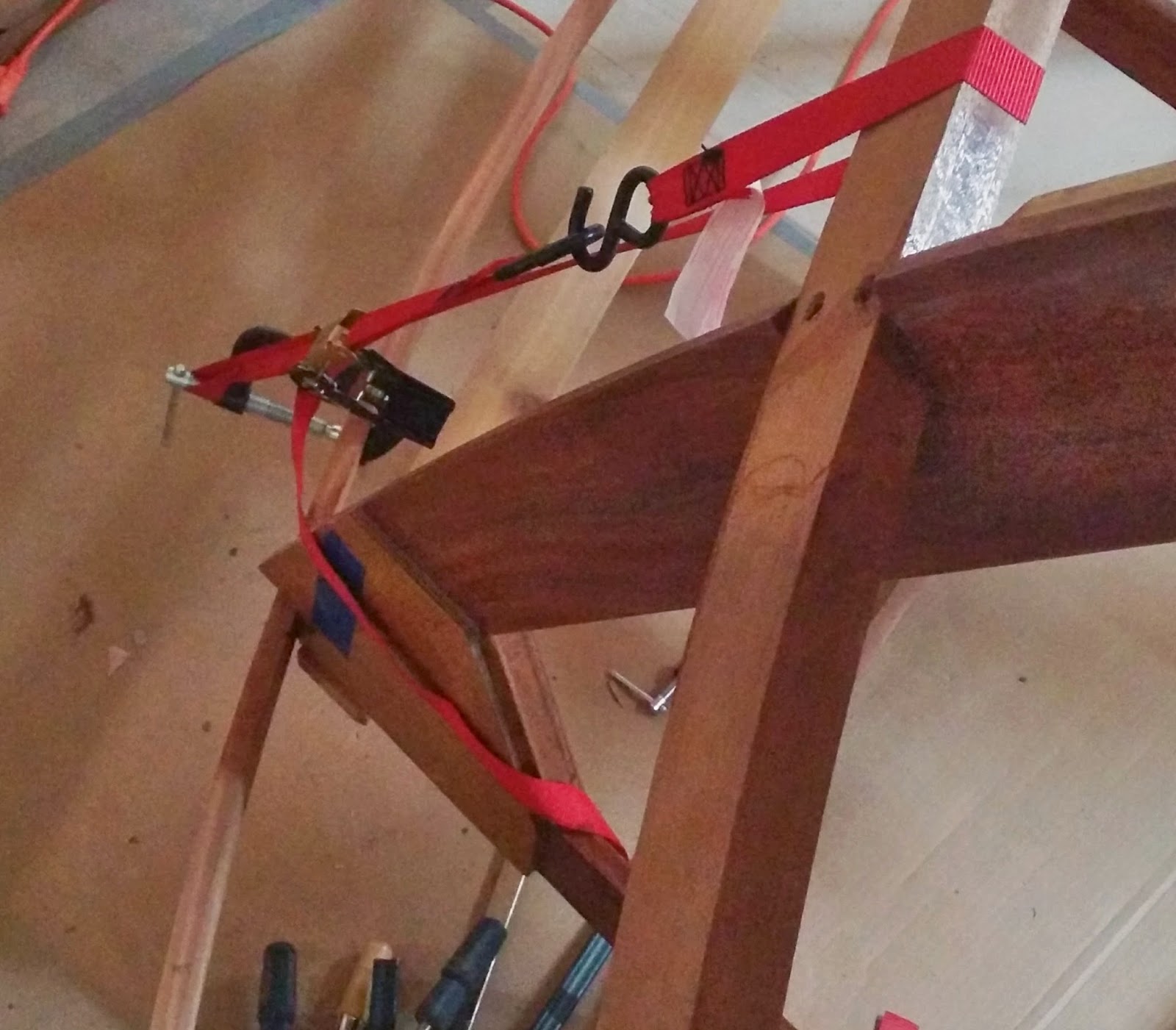
In the first photo, you can see the sheer attached to the breasthook. I tried my clamping jig but it broke as soon as I applied pressure with the clamps. So I ended up using wood screws to hold the sheer in place while the epoxy cured.
In the second and third photos, I am using the straps and the clamp to impart a slight twist to the sheer in order to get it to line up with the notch in frame 6. Between frames 5 and 6, the only difficulty was having to pull up on the sheer and holding it there while the epoxy in the notch of frame 5 cured. The straps helped here as well.
The remaining connections were straightforward and accomplished on the third night.
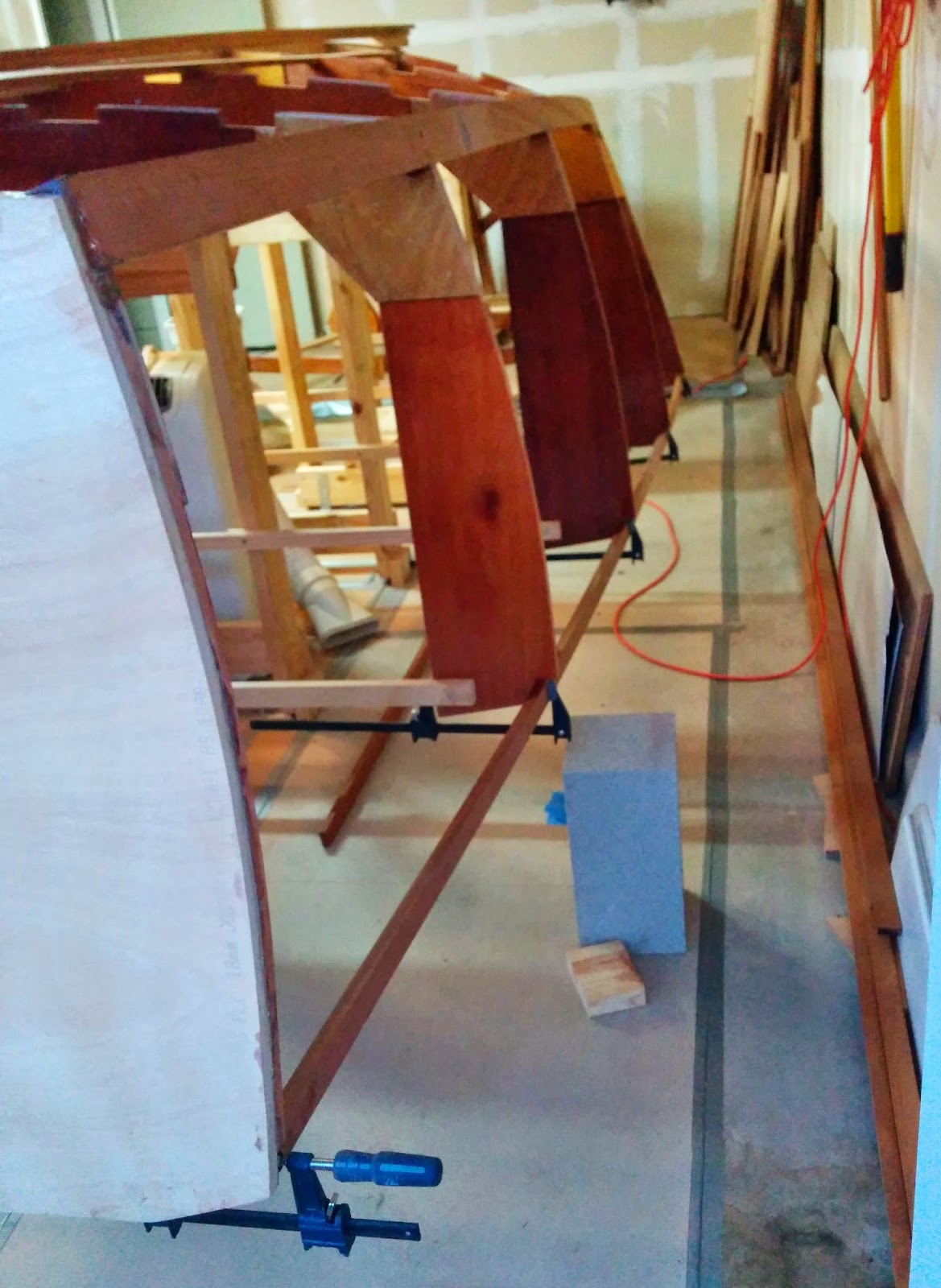
What remained to do was to re-steam the second lamination for the port side (because the original steamed wood had somewhat straightened out). I also extended it with a scarf joint. I wanted to insure that the scarf joint of the first lamination was not in the same place as the scarf joint on the outer lamination. So I made the joint on the second lamination further towards the bow.
Unfortunately, I thought I could trim the aft end of the second lamination before placing it on top of the first lamination. I simply placed it in the notches on the starboard side and made a cut beyond the end of the transom figuring that there would be more than enough excess.
Pride hit number 2: What I failed to consider was that the second lamination had to travel a longer curve because it was on the outside. So when I clamped it into position over the first lamination, I came up short of the transom by a good 6 inches. I ended up splicing in a second shorter piece (again using a scarf joint) so that the part was long enough.
Now the weather in the Austin area is rather warm and we are already hitting 90 degree days . I knew that if I tried to glue up the second lamination at the end of a warm day, that I was going to have problems with the epoxy curing on the forward parts of the sheer before I had completed attaching the aft portions.
So I elected to get up early this morning (3:30 AM) and accomplish the glue up before going to work. I had repaired my broken clamping jig and had everything ready to go this morning. However, the jig broke again and I was forced to use wood screws to hold the front of the sheer in place.
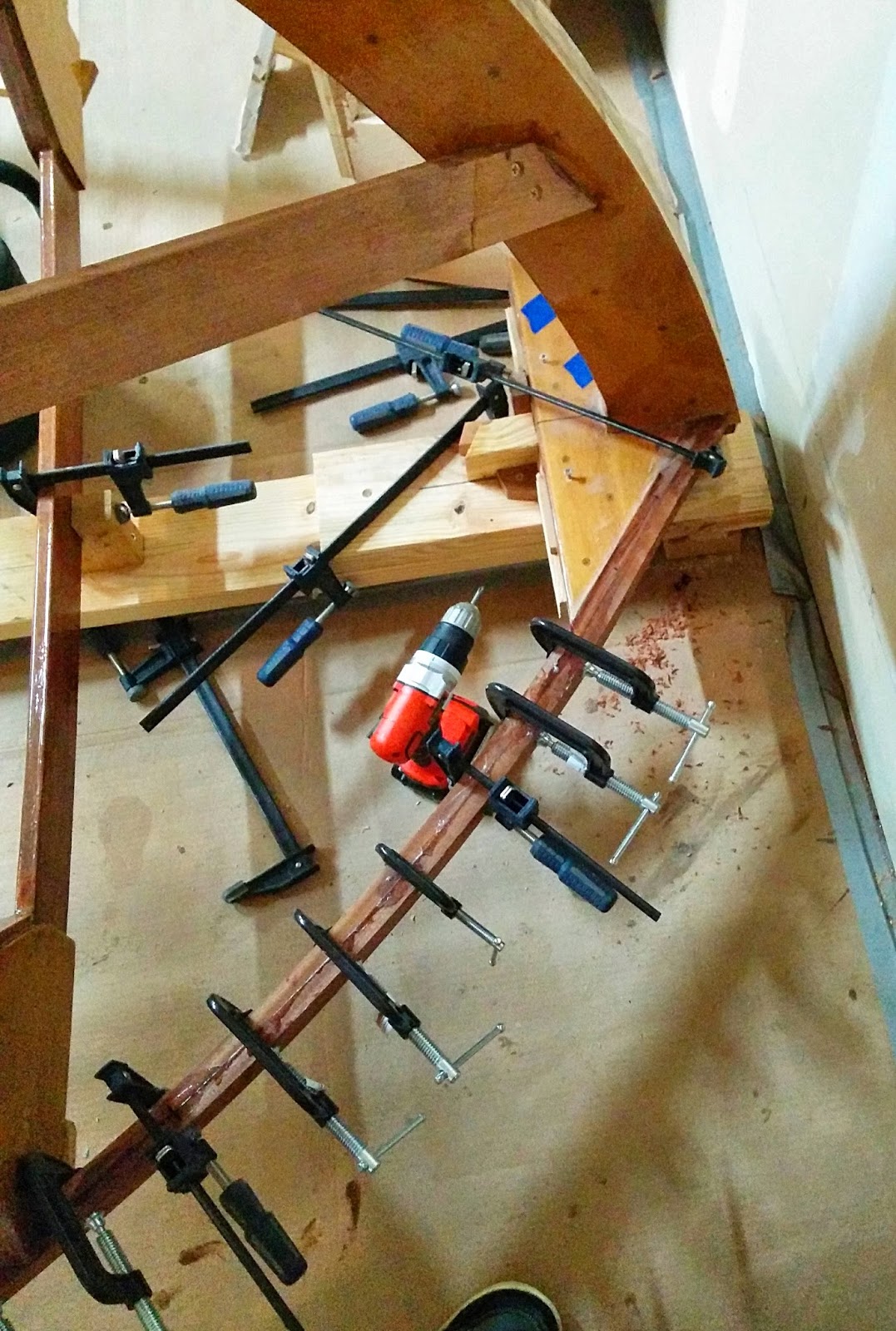
Now the sheer is supposed to get wood screws so adding them now is not a problem, But having to contend with the broken clamping jig slowed me down and I was already worried about getting everything done before the epoxy began to cure.
But the rest of the process went smoothly. I would apply thickened epoxy to approximately 6 feet of sheer at a time, and then clamp it into position. Then I moved on to the next section until I reached the end of the boat.
I initially only applied clamps in strategic locations to hold everything together until I was done applying epoxy. Then I went back and added clamps every 6 inches. There were approximately 60 clamps in position when I was completed.
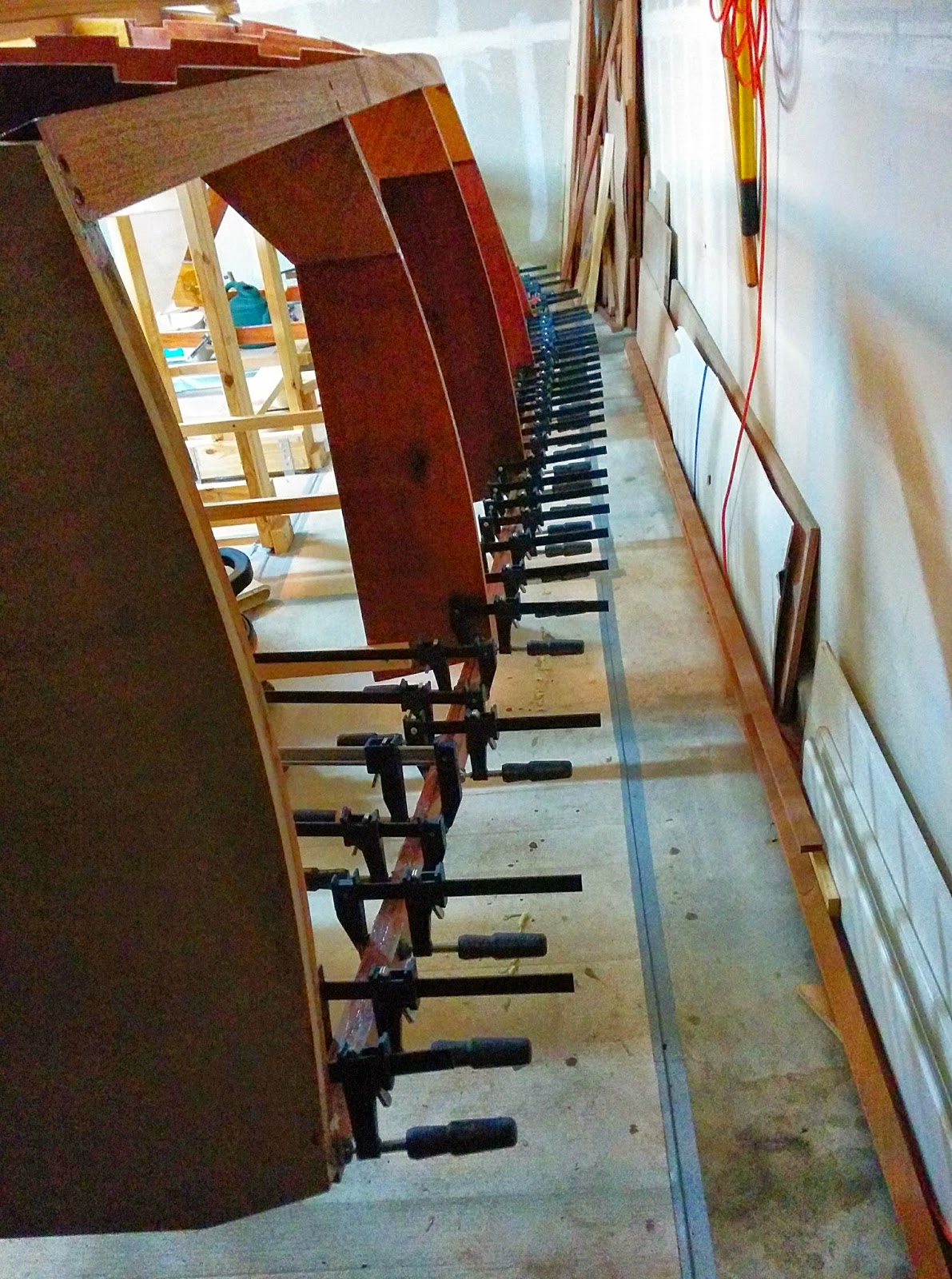

Afterwards, using a couple of tongue depressor sticks, I scraped off most of the glue that had squeezed out. By this time, the epoxy at the forward end was already setting up and was somewhat difficult to scrape off. Nonetheless, all of this was accomplished by 5:45 Am and I was able to get to work on time.
evening I removed the clamps and the sheer is ready for sanding and general clean up. Over the next several days, I will be repeating the process on the starboard side (hopefully avoiding any more mistakes).
I am starting to get close to the point of initial fairing for the side planking. I wont go into that now other than to say that it is another of those steps that I am dreading, especially at the bow where the stem curves downward.
I wanted to apologize for the lack of photos in this posting, but there isnt much to the process of attaching the sheers.
At any rate, I now have one side completed except for some clean up and you can really see the shape of the hull. is easily viewable in person , but unfortunately, not so easy to show using photos because I cannot get far enough back from the boat to get the entire hull in the shot.
So until next time, take care.
Sheer Work Continues
Getting the sheers on the boat should have been easier than adding the chines. After all, the wood is thinner and more flexible. Steaming was easier because less mass needed to be heated. Curves created through steaming held their shape better than that of the chines.
But instead, the sheer presented their own challenges. Let it be understood that I am not complaining here. Rather, I am remarking on the necessity of adapting and working through problems and difficulties as they occur.
particular process started off well. I had steamed a second piece of lumber and bent it. It fit pretty good around the breasthook, and when I added the extra length via a scarf joint, I was able to easily bring the far end around to the boat.
The first challenge I noticed was that the angle of the breasthook sides and the notches made it difficult to line up the sheer between the breasthook and frames 6 and 5. But by clamping the wood to the breasthook, I determined that I could work in stages and get the wood to line up. Therefore I decided to glue the first lamination to the breasthook only, and then over the next several days, glue the lamination to single frame points. would allow me to take advantage of the rigidity of the already glued on sections and adjust the loose end as I went.
I accomplished this first glue up and then proudly displayed the photo for all to see. Pride hit number 1; a friend on the Glen L builders forum pointed out that the sheer appeared to be too far forward. If I were to have continued and glued the second lamination on at this point, it would have extended out past the breasthook.
In other words I had missed that I needed to have the sheer set back enough so that when the front of the stem was faired at an angle, the line from the faired stem would flow into the sheer. The way I had it mounted would have required me to remove nearly all the second lamination at the front of the boat. Of course this was unacceptable.
Examining the problem for awhile, I realized that the breasthook itself was mounted too far forward on the stem. looked like a disaster of major proportions and I was quite upset about this for an evening. But later after examining it some more and with the suggestions from the friend on the forum, I elected to cut the forward side of the breasthook back the necessary amount (about 5/8 inch).
First I had to cut the glued on sheer away from the breasthook. The Bosch multi-tool I recently purchased was perfect for doing this as well as cutting the breasthook back. After accomplishing this I hit the forward face of the breasthook with a belt sander to smooth it out. I could now reattach the sheers to the breasthook and they would be set back the correct amount.
Of course, the breasthook is now smaller and I intend to reinforce it on the back edge after the sheers are all in place. I will be laminating a solid piece of mahogany to the back edge of the breasthook between the sheers. should effectively restore any strength lost when I trimmed the forward edge.
So I re-attached the sheer to the breasthook and over the next three days, attached first frame 6, then frame 5, and then the remaining frames to the aft end of the boat. I adjusted the sheer each day as I attached it to another frame. The following photos show a bit of this process.
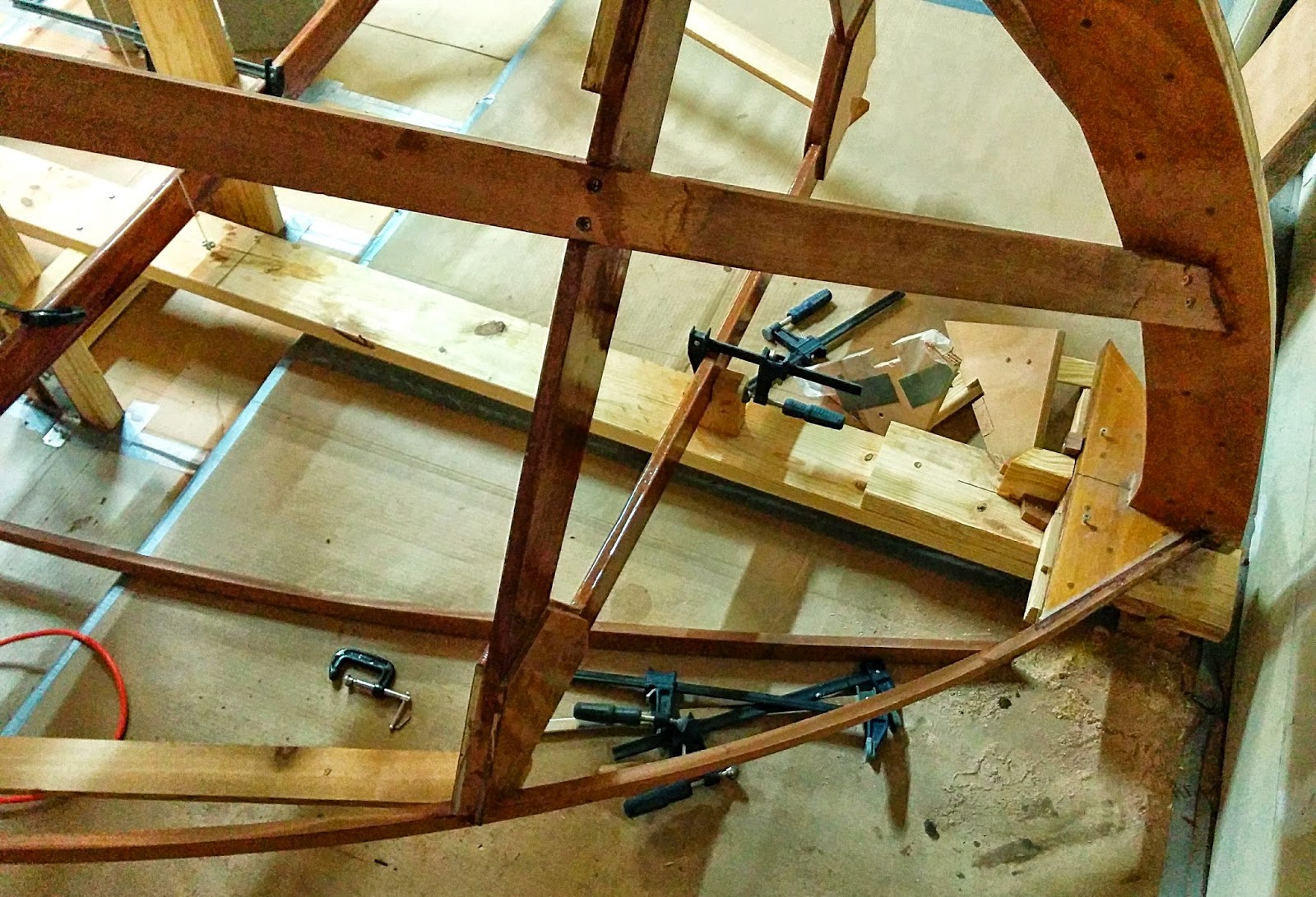
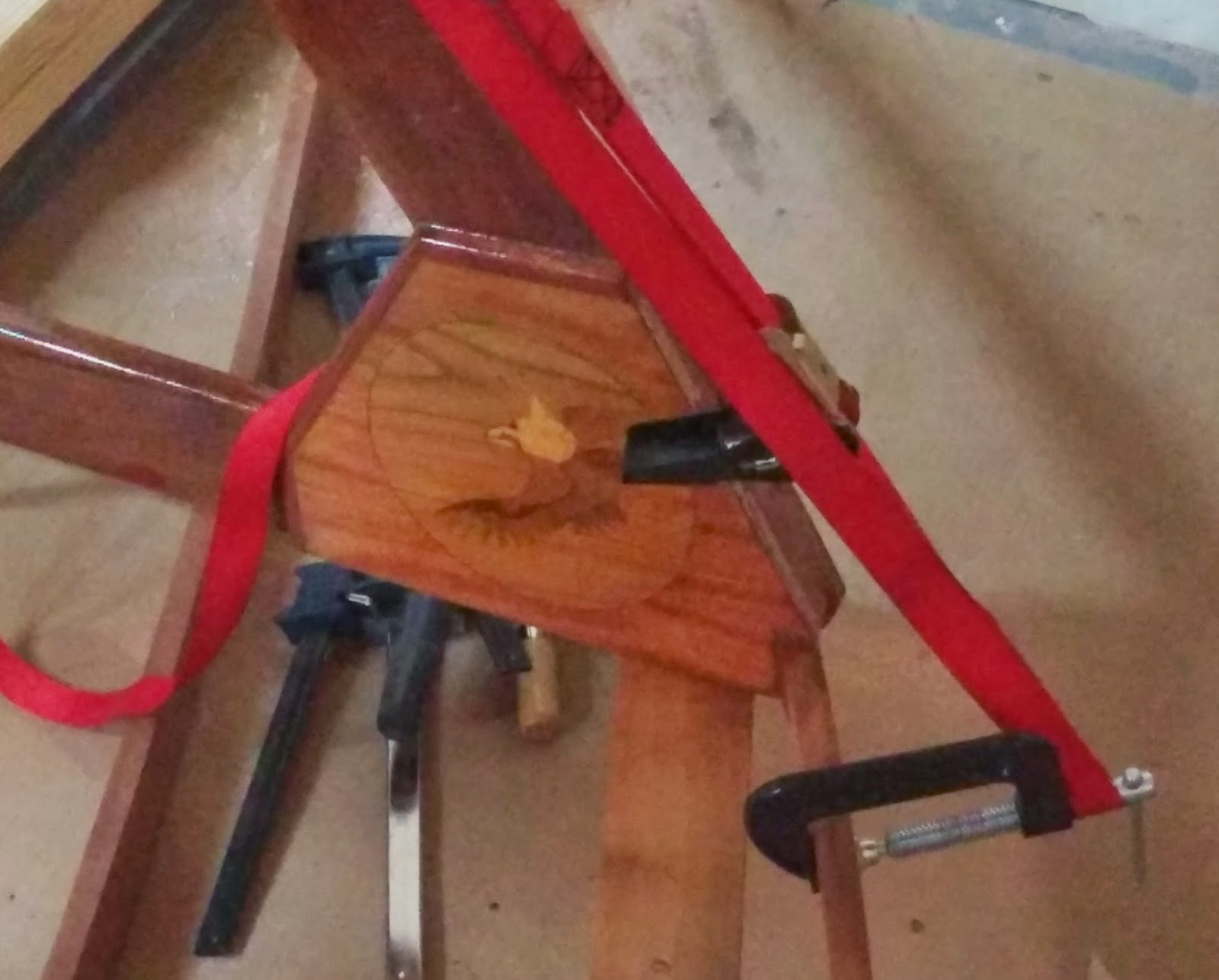
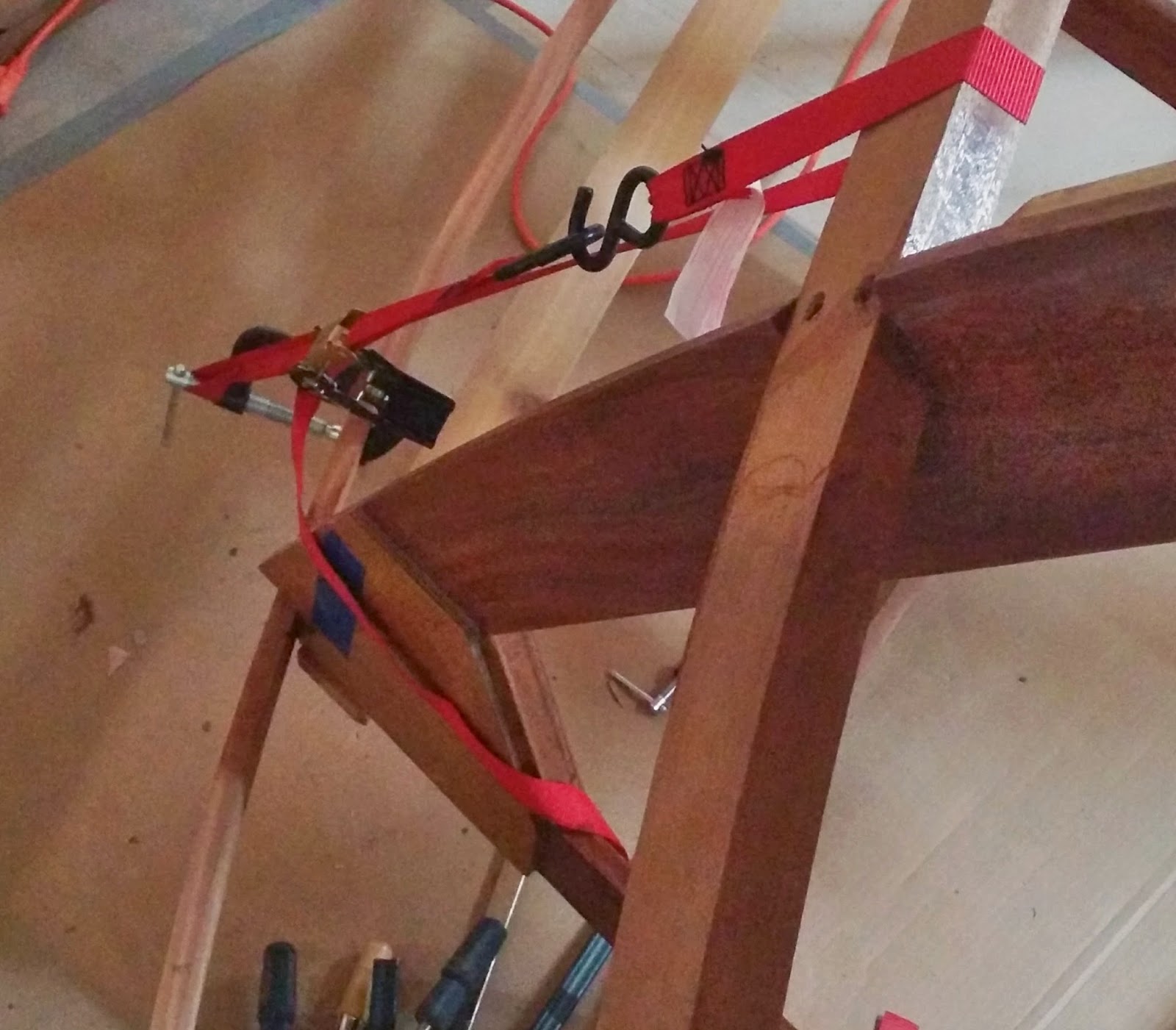
In the first photo, you can see the sheer attached to the breasthook. I tried my clamping jig but it broke as soon as I applied pressure with the clamps. So I ended up using wood screws to hold the sheer in place while the epoxy cured.
In the second and third photos, I am using the straps and the clamp to impart a slight twist to the sheer in order to get it to line up with the notch in frame 6. Between frames 5 and 6, the only difficulty was having to pull up on the sheer and holding it there while the epoxy in the notch of frame 5 cured. The straps helped here as well.
The remaining connections were straightforward and accomplished on the third night.
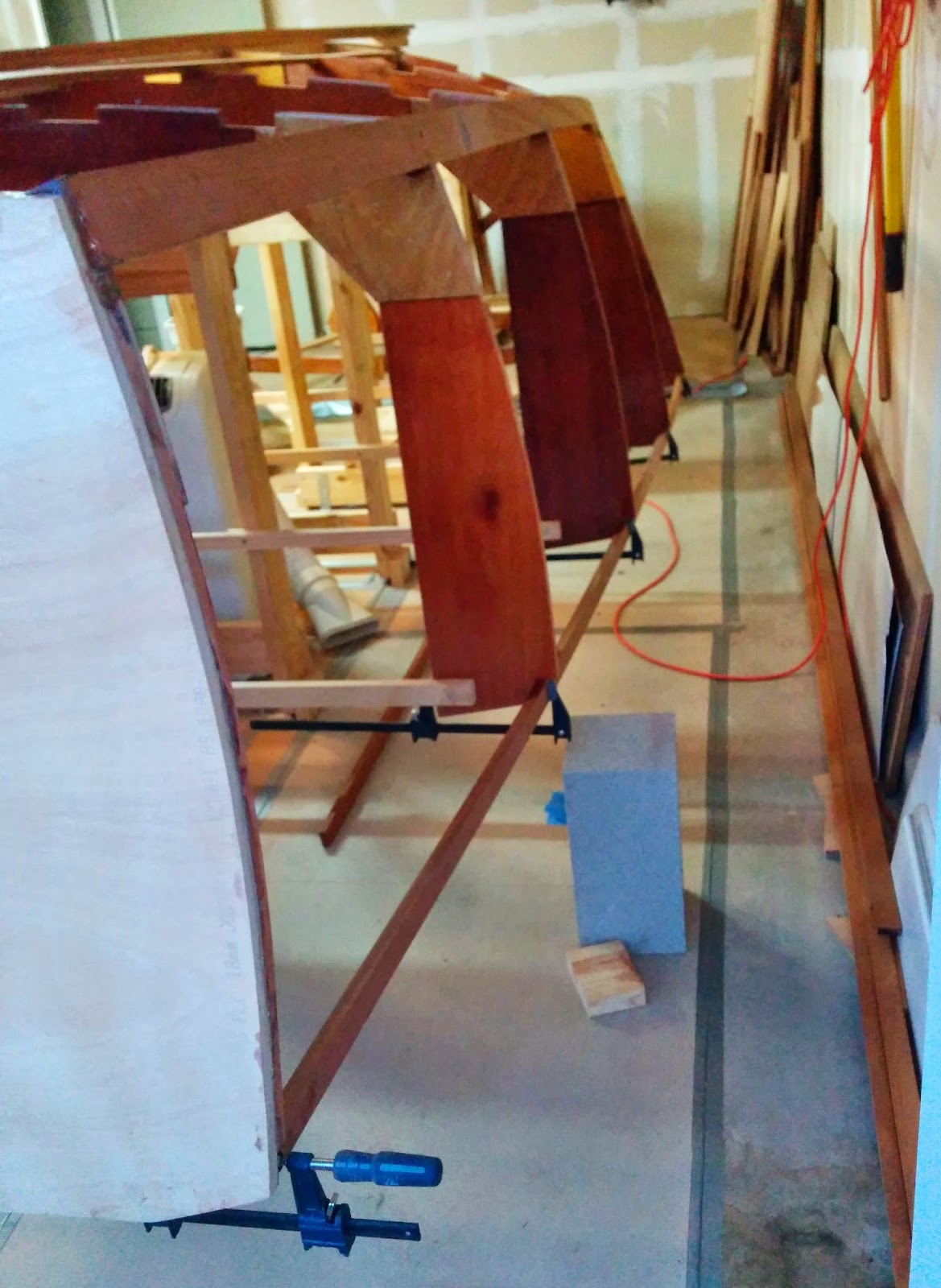
What remained to do was to re-steam the second lamination for the port side (because the original steamed wood had somewhat straightened out). I also extended it with a scarf joint. I wanted to insure that the scarf joint of the first lamination was not in the same place as the scarf joint on the outer lamination. So I made the joint on the second lamination further towards the bow.
Unfortunately, I thought I could trim the aft end of the second lamination before placing it on top of the first lamination. I simply placed it in the notches on the starboard side and made a cut beyond the end of the transom figuring that there would be more than enough excess.
Pride hit number 2: What I failed to consider was that the second lamination had to travel a longer curve because it was on the outside. So when I clamped it into position over the first lamination, I came up short of the transom by a good 6 inches. I ended up splicing in a second shorter piece (again using a scarf joint) so that the part was long enough.
Now the weather in the Austin area is rather warm and we are already hitting 90 degree days . I knew that if I tried to glue up the second lamination at the end of a warm day, that I was going to have problems with the epoxy curing on the forward parts of the sheer before I had completed attaching the aft portions.
So I elected to get up early this morning (3:30 AM) and accomplish the glue up before going to work. I had repaired my broken clamping jig and had everything ready to go this morning. However, the jig broke again and I was forced to use wood screws to hold the front of the sheer in place.
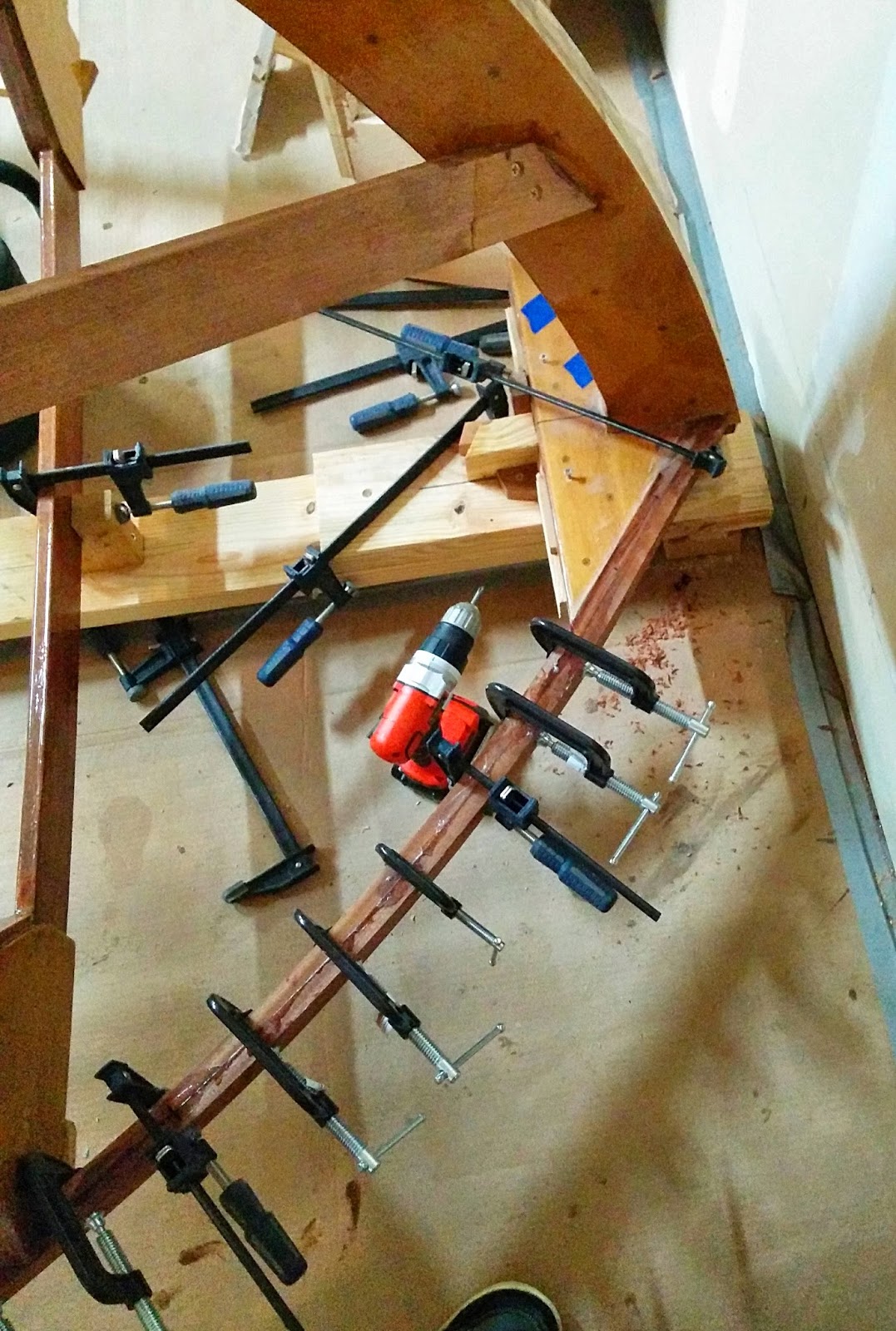
Now the sheer is supposed to get wood screws so adding them now is not a problem, But having to contend with the broken clamping jig slowed me down and I was already worried about getting everything done before the epoxy began to cure.
But the rest of the process went smoothly. I would apply thickened epoxy to approximately 6 feet of sheer at a time, and then clamp it into position. Then I moved on to the next section until I reached the end of the boat.
I initially only applied clamps in strategic locations to hold everything together until I was done applying epoxy. Then I went back and added clamps every 6 inches. There were approximately 60 clamps in position when I was completed.
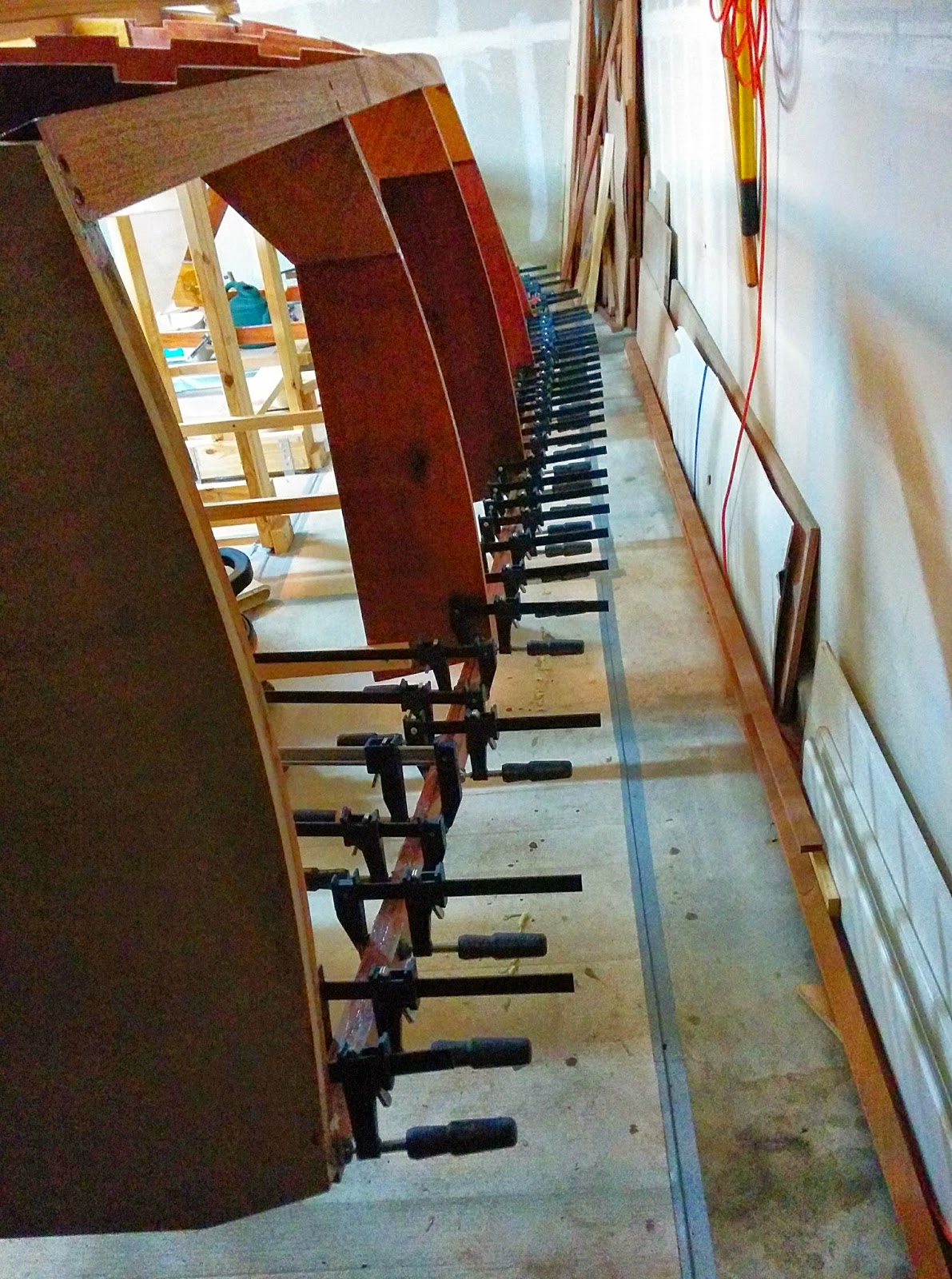

Afterwards, using a couple of tongue depressor sticks, I scraped off most of the glue that had squeezed out. By this time, the epoxy at the forward end was already setting up and was somewhat difficult to scrape off. Nonetheless, all of this was accomplished by 5:45 Am and I was able to get to work on time.
evening I removed the clamps and the sheer is ready for sanding and general clean up. Over the next several days, I will be repeating the process on the starboard side (hopefully avoiding any more mistakes).
I am starting to get close to the point of initial fairing for the side planking. I wont go into that now other than to say that it is another of those steps that I am dreading, especially at the bow where the stem curves downward.
I wanted to apologize for the lack of photos in this posting, but there isnt much to the process of attaching the sheers.
At any rate, I now have one side completed except for some clean up and you can really see the shape of the hull. is easily viewable in person , but unfortunately, not so easy to show using photos because I cannot get far enough back from the boat to get the entire hull in the shot.
So until next time, take care.
Subscribe to:
Post Comments (Atom)
No comments:
Post a Comment